by Harley Beattie, Knowledge Transfer Partner Associate. Read Harley's previous ECM Horizon Scanning piece here .
Context
When working with start-ups, Engineering Change Management (ECM) is often among the first processes identified as required and implemented by the QR_ team. ECM is easily overlooked in early-stage start-ups as communication between stakeholders is usually straightforward, and the organisation may not yet be at a stage where changes have downstream impacts in the production world. However, it is vital to establish ECM at this early stage to ensure changes are requested, reviewed, and implemented in a controlled manner, minimizing risks to initial production and product launch.
Failure to manage engineering change from the outset can result in incorrect orders, missing parts, incompatible components and ultimately lead to significant costs and delays. QR_ have repeatedly observed significant lineside issues in clients who have neglected to implement change management during the early development phase. In one small organisation, QR_ was able to attribute over 30% of lineside issues to a lack of release and change management. Bill of material (BOM) errors, design issues and drawing revisions were the top causes of these issues, all of which could have been mitigated via release and change management.
Unfortunately, ECM is not something that can be bought off the shelf, nor is designing a bespoke process an isolated task. There are numerous factors to account for, including interfacing processes, system architecture, scalability, company culture and more. As such, there are a number of prerequisites that must be in place before effective ECM can be designed and implemented. Failure to ensure these are in place at the minimum required level can result in ineffective, poorly controlled change management. Furthermore, the process could be subject to significant redesign as core elements are introduced retrospectively, reducing stakeholder trust and buy-in.
This paper outlines the key prerequisites that should be in place for ECM to function effectively. For each area, a minimum and ideal requirement specification has been outlined. Although having the ‘ideal’ requirements in place will help ECM function more effectively from day one and reduce process iterations, making decisions and implementing change management quickly is the priority to gain control of the change throughput. Therefore, a balance must be struck between speed and creating an ideal environment for implementation.
People
Top priority when preparing to introduce an ECM process to an organisation is aligning the entire team around how to manage change, and how this may evolve over time. Once these fundamental principles are agreed, and there is buy-in across the key stakeholders, the process can be developed and implemented based on these principles. This will mitigate delays due to disagreement or misunderstanding.
Secondly, the process users must be aware of the incoming process, and accept the introduction of new responsibilities, including any additional administrative work. Not all employees in a start-up will have previous experience with ECM, and may not realise that multiple releases are required before the design stabilises. It is vital to empower these users with the basic principles of ECM, and justification for its introduction to gain buy-in from the beginning.
Key process roles must have clear ownership. This should be communicated clearly at an early stage, to establish where there are responsibility gaps or confusion, and gain buy-in from key stakeholders before any changes are made. Key roles include:
Change controller. As this is a new role, there must be provisions in place to assign ownership prior to ECM implementation. This may be external initially, to ensure the correct expertise is available to guide process implementation and establish organisation as usual tasks. The responsibilities for this role should be outlined in detail to facilitate role assignment.
Engineering: Responsible for technical design changes and the primary initiators of major change. Process cannot operate without their involvement and it is therefore important to secure buy-in before the process is introduced.
Manufacturing: Representative to ensure changes will be introduced in production world appropriately e.g. build timing plans and instructions reflect change, stock switch over plans etc.
Procurement (liaising with suppliers): Vital for when programme matures from digital to physical development. Must be involved to ensure orders are placed and costs are managed.
Case study: green energy start-up
So how is this achieved? Earlier this year QR_ successfully established ECM in an innovative green energy start-up within a compressed 6-week time frame. Being able to design and successfully implement ECM within this time frame is attributable to the engagement and support of the client team. By educating on the need for ECM, the organisational benefits offered (de-risking product launch), and the basic mechanics of the process, key stakeholders were identified and engaged from an early stage. Collaborative workshops resulted in a process design that stakeholders understood well and aligned their expectations to. As the organisation is small, some roles such as manufacturing owner were not yet officially in place. This was identified, and an appropriate temporary representative assigned responsibility, which in turn was considered during the design for the MVP and accelerated the urgency to recruit for these specific roles.
People summary
Minimum:
- Basic level of buy-in from key stakeholders.
- High-level understanding of ECM and associated impacts and some alignment on high-level approach.
- Awareness of need for a change controller and PDM function.
- Representatives available for key approvals roles; engineering, purchasing, manufacturing.
Ideal:
- Organisation wide buy-in to process.
- Knowledgeable of ECM, its benefits and organisation impact.
- Widespread alignment on high-level approach.
- Plans for creation of change controller role both short term and long term.
- Understanding of R&R’s of process stakeholders who are willing to participate in process.
Data
A base level of Master Data Management (MDM) must be in place so that ECM can utilise it to function effectively. This is the most important technical prerequisite for an effective ECM system, and should be prioritised. Specifically, two areas of data should be in place prior to ECM implementation:
1. Part numbering system
One of the first pieces of master data that must be in place is a part numbering system. Part numbers provide unique identifiers for components and assembly structures, as well as tooling and software when required. Having a unique identifier is crucial to track change data and maintain version control of individual parts.
2. Bill of Materials
Another area of MDM that must be addressed is the creation of a Bill of Materials (BOM). One of the core functions of ECM is to ensure the accuracy of product data is maintained, including assembly structures, drawing revisions, part quantities, cost and other attribute data. The BOM provides a centralised record of product data, and act as a single source of truth for part maturity and latest approved part revisions. Having this data accurately reflected in a BOM ensures changes can be implemented downstream with confidence, and there is transparency surrounding part versioning and attribute data. In addition to having a BOM structure in place, the data captured within it must be accurate and stable (to a reasonable degree) before ECM can be implemented, hence a BOM validation should take place prior to formal ECM process implementation.
Case study: green energy start-up
As a relatively new, small-scale organisation, data management was a low priority, and as such no master data or data plumbing was in place prior to QR’s involvement.
As outlined above, the priority was to create part numbers and a basic BOM structure. Limited by existing systems (or lack thereof), a simple sequential part numbering system was established, and a flat structured spreadsheet BOM created. A manual change log was established, and a temporary BOM owner assigned from the QR team. This ensured that all changes were captured from the first day on project, and data quality and confidence was improved with immediate effect, as well as stabilising the BOM data in preparation for ECM. Over 80% of the BOM line items had data changes tracked against them within the first 10 days, driven by QR’s BOM validation exercises. In parallel to this activity, an ECM process was designed and built into existing systems, enabling the rapid implementation of an effective process.
Data summary
Minimum:
- A controlled, sequential part numbering system. Care must be taken via version control to link up-revisions, as the part-number itself may not have ability to indicate maturity or versioning.
- A basic version-controlled BOM structure (can be as simple as a spreadsheet) capturing core master data such as part numbers, descriptions, cost, weight etc.
- BOM validation exercise to baseline data quality.
Ideal:
- An intelligent part numbering system with up-versioning ability and maturity indication (prototype vs production etc.)
- A structured Engineering BOM (EBOM) and Manufacturing BoM (MBOM) with comprehensive data capture, maintained in a system with capability to interface with CAD structure and the chosen release system.
- Full BOM validation exercise to maximise accuracy and completeness.
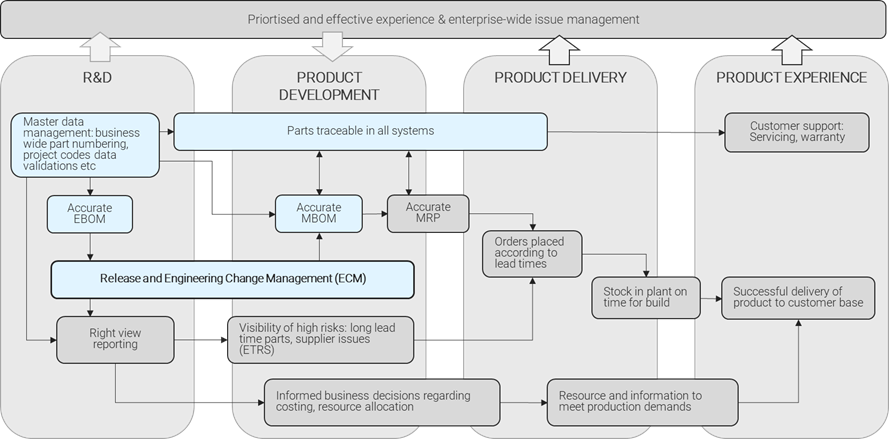
Figure 1: Basic data flow required to get a product to market, highlighting master data as the foundation for ECM
Systems
Next, focus should be turned to the available systems. For ECM to work effectively, there must be system architecture in place with the ability to;
- Version control designs
- Raise and track changes
- Facilitate approval workflows
If there is no appropriate system architecture in place, the timeline and scale of investment should be discussed prior to commencing an ECM project, so appropriate intermediate solutions can be implemented. It is important to have a basic form of change management operational as soon as possible to de-risk current activity. However, this could vary significantly depending on the system roadmap. For example, if there are plans to implement a sophisticated PLM system architecture imminently, basic manual control via email and spreadsheet may suffice for the short interim period, whilst preparing to migrate to the new system. However, if there are no immediate plans for system investment, and no suitable architecture in place, an interim product which meets the necessary requirements may need to be purchased.
Systems summary
Minimum:
- Visibility of current and future plans for system investment
- Ability to version control designs
- Basic workflow software to raise and track changes (SharePoint, ticketing system, etc)
Ideal:
- PLM system in place/purchased and ready to be configured, or clear timeline to do so
- System constraints known and can be accounted for in detail design
- APIs to interface with CAD, BOM and other supporting systems
- Functionality to facilitate ‘smart’ workflows e.g. approvers and workflow selected based on release attributes, approver matrices etc.
Process
As ECM is often one of the first processes to be introduced into a organisation, there are fewer prerequisites in terms of supporting processes. Upstream and downstream processes such as Issue management, Plan For Every Part, and MRP should be considered when designing ECM to ensure data flow between each is effective, aligned and automated where possible.
In terms of ECM itself, agreement should be made regarding the fundamental concepts of the process before detailed design and development. This may be challenging in a situation where senior stakeholders from multiple backgrounds hold strong options on what is considered best practise. Key aspects that should be discussed at a high level initially include:
- High level definition of change types (major/minor/software etc).
- Rules surrounding interchangeability
- Strategy for approval process: Push vs Pull
- Balance between agility and adherence
Process summary
Minimum:
- Basic agreement on several core aspects of change
- Acknowledgement of surrounding processes and awareness of interfacing mechanism with ECM
Ideal:
- Alignment on industry standard for ECM with clear vision for high level approach
- Willingness to compromise and discuss approach to reach agreement on details at later stage
- Understanding of surrounding processes and with plans to integrate with ECM in later process development
Conclusion
As outlined, there are several key prerequisites to ensure the successful design, development and implementation of an ECM process. Whilst it is desirable to have the ‘ideal’ environment established in preparations for ECM, establishing control of the data flow and key repositories as quickly as possible is priority, to ensure milestones such as launch are not delayed due to poor data management or visibility. Providing the minimum required foundations are present, ECM can evolve and become more nuanced as the product and the company develop.